在大學生電動方程式賽車中,傳動系統直接影響著賽車的性能。近年來,四電機輪邊減速器系統在中國大學生電動方程式大賽(Formula Student Electric China, FSEC)賽車中的應用逐漸引起關注。該系統通過在每個輪邊安裝一個電機,實現四電機獨立驅動,從而提高賽車的操控性和穩定性,同時減少傳動損失,提高能效。本文對該系統進行深入研究,以期為我國大學生電動方程式賽車技術的發展提供理論支持和實踐指導。
1、設計原理
電機輸出端與太陽輪連接,同時與太陽輪之間通過花鍵配合,電機的輸出端輸出扭矩而帶動太陽輪旋轉時,太陽輪與大行星輪的嚙合作用促使大行星輪和小行星輪產生自轉,同時由于小行星輪與安裝在輪轂內壁上的齒圈相互嚙合,最終在自轉驅動力的作用下,行星輪將帶動齒圈使其沿著與太陽輪旋轉相同的方向轉動,齒圈帶動輪轂轉動。電機輸出的動力經過減速器后,轉速降低,扭矩增大,最終通過輪轂輸出。
2、傳動比的計算
參數范圍
這里將計算所涉及的參數匯總,如表 1 所示。
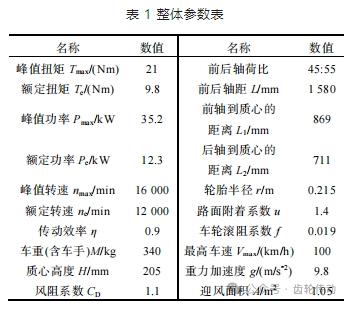
1)根據最高車速確定傳動比下限,經式(1)計算可得 i ≥12.97。

2)根據最大加速度確定傳動比上限。查詢賽事官網上公布的 2023 賽季 FSEC 直線加速成績可知,75 m 直線加速的最好成績為 3.8 s,因此,加速預設成績為 3.85 s,相關公式為

式中,x=75 m,Vmax=100 km/h=27.78 m/s,t=3.85 s。
聯立式(2)-式(4)便可以計算出所需要達到的加速度約為 12.1 m/s2。此時賽車所需的最大驅動力 Ftmax 為 4 723.4 N,其計算公式為

為確保賽車始終能夠達到最大加速度,式(5)中 V=Vmax=100 km/h。地面對輪胎的最大附著力與滾動阻力之和為

根據賽車所需的最大驅動力計算傳動比上限為 13.433,計算公式如下:
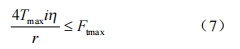
參數選擇
這里綜合考慮輪轂減速器的安裝方式,傳動比的范圍以及輪輞、制動盤對減速器大小的限制,并最終確定減速器的內部布置形式,如圖 1 所示。
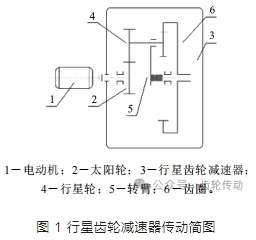
根據計算出的傳動比取值區間,選擇出多組行星齒輪組的齒數,如表 2 所示。
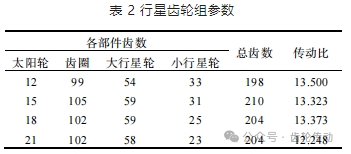
考慮到太陽輪為驅動輪,其齒數越大強度越高;行星齒輪組的總齒數越小,其加工成本越低;傳動比要盡量接近傳動比上限,保證驅動力。根據以上設計要求,確定行星齒輪組的齒數如表 2 第三組數據所示,同時確定行星齒輪組的齒寬,如表 3 所示。
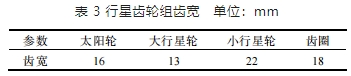
經計算可知,輪轂減速器的減速比為 13.373。聯立式(1)、式(5)、式(7),并代入減速比 i=13.373,計算得出賽車的實際最高車速為 97 km/h,實際最大加速度 a=12.04 m/s2,再將 Vmax 和 a 代入式(2)-式(4)可以計算得到 75 m 直線加速的成績約為 3.9 s。
3、齒輪模數的確定
太陽輪與大行星輪的最小模數
根據齒根彎曲強度初算齒輪模數:
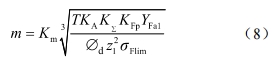
式中,Km 為算式系數,對于直齒輪傳動取 12.1,斜齒輪傳動取 11.5,此處取 12.1;T1 為嚙合齒輪副中小齒輪的名義轉矩(功率分流后的值),取 7 Nm;KA 為使用系數,取 1.25;KΣ為綜合系數,取 1.8;KFp 為計算彎曲強度的行星輪間載荷分布不均勻系數,取 1.75;YFa1 為小齒輪齒形系數,取 2.35;∅d 為小齒輪的齒寬系數,取 0.9;z1 為齒輪副中小齒輪的齒數,取 18;σFlim 為實驗齒輪彎曲疲勞極限,取 1 100 N/mm2。將上述數據代入式(8)進行計算,得到在太陽輪與大行星輪的嚙合副中齒輪的模數最小為 0.71。
小行星輪與齒圈的最小模數
同理可以計算出小行星輪與齒圈的最小模數,在這一對嚙合副中,Km=12.1、T2=22.944、KA=1.25、KΣ=1.7、KFp =1.7、YFa1=2.18、∅d=0.9、z1=25,將數據代入式(8)便可計算得到,小行星輪與齒圈的最小模數為 0.8。
由于齒輪模數會影響齒輪的大小,從而影響減速器的大小,且輪輞的大小又限制了減速器的大小,同時也為了保證齒輪的強度,所以最終確定輪轂減速器的齒輪組模數均為 0.8。
4、設計輪轂減速器的三維模型
太陽輪設計
該減速器中太陽輪需兼具聯軸器的作用,所以這里將其加長,在一端設計了與電機輸出軸上齒型花鍵相互配合的內齒形花鍵,同時在其兩端都設計了用于安裝軸承的擋肩,以提高其高速旋轉時的穩定性。詳情如圖 2 中 9 所示。
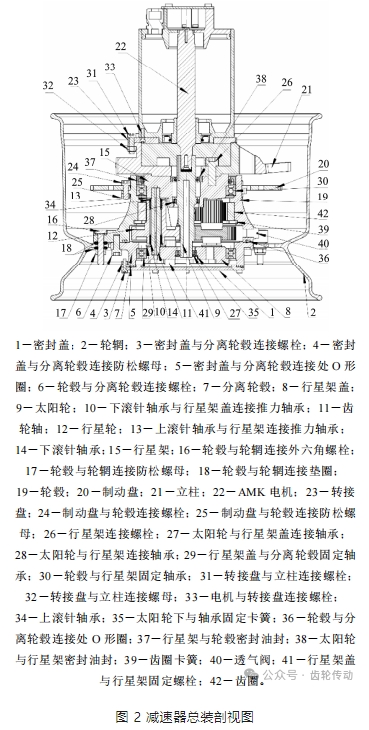
行星架設計
行星架在減速器內部起到支撐減速器的作用,這里將行星架分為兩部分,兩者通過過渡配合與螺栓實現固定連接。設計過程中需要綜合考慮行星齒輪的中心距、太陽輪的安裝、齒圈和輪轂的大小以及其自身的安裝和整體的密封等。同時由于行星架外徑的限制,行星輪的軸承無法直接安裝到行星架上,所以將滾針軸承設計安裝到行星輪的內部,搭配齒輪組與推力軸承,實現了行星輪的安裝與旋轉。詳情如圖 2 中 8、12、15 所示。
輪轂設計
輪轂是減速器零件集成安裝平臺,設計過程中需要綜合考慮零件之間的安裝,避免干涉,并兼顧其內部的密封。此外將輪轂拆分為輪轂和分離輪轂兩部分,兩者通過過盈配合與螺栓實現固定連接,同時在兩者連接處安裝 O 型圈增強密封效果。這樣的設計使得軸承可以分別裝在兩個輪轂上,降低裝配過程的復雜度,詳情如圖 2 中 7、19 所示。
立柱設計
立柱是懸架系統與輪邊系統連接的媒介,設計過程中需要綜合考慮減速器、電機、制動卡鉗的安裝,與行星架之間通過過盈配合與螺栓實現固定連接。同時由于電機的安裝孔位置特殊,電機無法直接與立柱相連。所以設計了轉接盤,裝配時可以首先將電機連接到轉接盤上,再將轉接盤連接到立柱上,詳情如圖 2 中 21、23 所示。
5、零部件的受力計算與強度校核
1)零部件的受力計算如圖 3 所示。
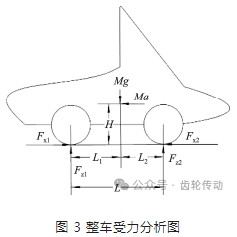
將計算出的整車最大加速度 a=12.1 m/s2,代入式(9)計算地面對兩后輪的支撐力 Fz2:
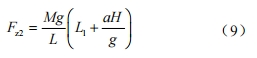
地面能夠提供給兩后輪的最大靜摩擦力 Fx2 為 3 312.96 N,計算公式為

根據式(9)、式(10)計算可知,當賽車以最大加速度 a 加速起步時,地面對后輪的作用力 Fz2=2 366.4 N,即單個后輪轂、后分離輪轂、行星架、行星架蓋的軸承安裝孔處,所受軸承載荷為 591.6 N。兩后輪的最大驅動力:

當賽車以最大加速度 a 加速起步時,根據式(11)可以計算出地面對后輪胎的摩擦力為 2 351.16 N,即單個后輪轂、后分離輪轂、行星架、行星架蓋的軸承安裝孔處所受的軸承載荷為 587.79 N。
2)齒輪組的受力計算。齒輪組的受力分析如圖 4 所示。
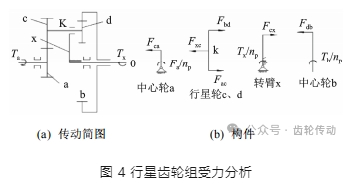
計算齒輪組受力所需的參數,當 Ta=Tmax= 21 Nm,行星輪個數 Np=3 時,齒輪 a-d 的分度圓直徑依次為 14.4、47.2、20、81.6 mm。行星輪 K 由 c(大行星輪)與 d(小行星輪)同軸構成一體,中心輪 a 的切向力為

中心輪 a 的轉矩為

行星輪 K 的切向力為
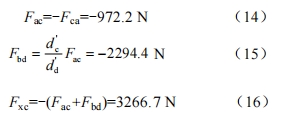
行星輪 K 轉矩為

轉臂 x 的切向力為

轉矩 Tx 為
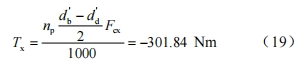
內齒輪 b 的切向力為

轉矩 Tb 為

當賽車以最大加速度 a 加速起步時,根據式(12)-式(21)可以計算出在單個輪轂減速器中,太陽輪所受扭矩為 21 Nm,行星輪所受扭矩為 22.944 N,行星架所受扭矩為 301.84 Nm,齒圈、輪轂所受扭矩為 280.84 Nm。
6、ANSYS 有限元分析
為了驗證零件結構設計與材料選取的可靠性,通過 ANSYS 有限元分析對零件進行強度校核。建立材料屬性如表 4 所示,并在 ANSYS 中對材料進行定義。

根據上文中計算的數據,對零件進行載荷約束,并讀取其等效應力圖,如圖 5-圖 7 所示。
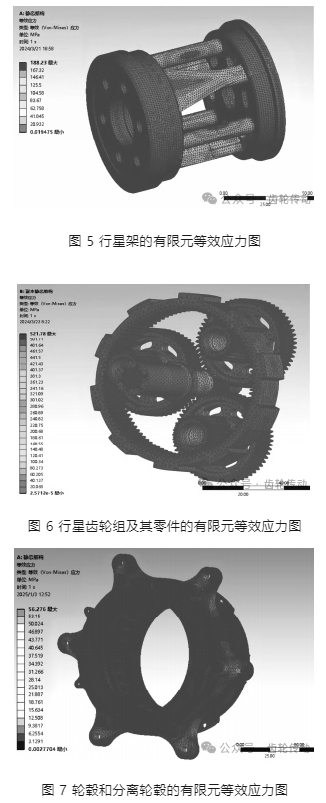
通過圖 5 最大等效應力與零件對應材料的屈服強度可知,對于采用 7075AL 為材料的零件安全系數均至少為 2.68,齒輪組中各個零件的安全系數也均超過 1.6,反映了零件結構和材料的合理,同時也驗證了參數計算階段結果的正確性。
7、結論
本文通過對 FSEC 賽車的四電機輪邊減速器系統的優化設計,得出以下結論:
1)在搭配四臺 AMK 電機的情況下,賽車的傳動比在 12.97~ 13.433 之間,均可滿足其在動力性上的需求。
2)為了降低輪邊系統在裝配過程中的復雜度,可以將內部集中裝配零件的殼體(輪轂)拆分成兩部分。
3)除齒輪組外,輪邊系統中的零件均可以采用 7075AL 為材料,其強度可以很好地滿足需要,同時質量較輕、加工難度小。
參考文獻略.