發動機依靠驅動齒輪與發動機飛輪盤外緣的飛輪齒圈相互嚙合來傳遞動力,進而啟動發動機。在發動機實際運行過程中,受設計、加工或裝配等因素的影響,可能會出現齒輪嚙合不佳的情況,或者由于齒根強度不足而引起斷齒、磨齒等現象,最終導致發動機故障。因此,深入分析飛輪齒圈斷裂原因,并提出有效的改進措施,具有重要的現實意義。
本文以某款2. 8 L柴油發動機的飛輪齒圈為研究對象,針對其斷齒問題,采用故障樹分析(FTA)法,從材料化學成分、硬度、金相組織、斷口以及齒圈強度等多個方面進行詳細檢測和分析,以期探明飛輪齒圈斷齒的根本原因,并為改進設計和制造工藝提供科學依據,從而有效提高飛輪齒圈的可靠性和耐久性,確保發動機穩定運行。
一、故障現象
根據2. 8 L發動機的市場故障信息統計,近3年來,飛輪齒圈頻繁出現斷齒故障,如圖1所示。出現斷齒情況的發動機行駛里程均在1萬km以內,屬于早期失效。由圖1可見,飛輪摩擦面無異常磨損和燒蝕,其背面也無異常狀況;齒圈中有1個齒從根部斷裂,其相鄰的2個齒有輕微磨損,其余齒面無磨損。
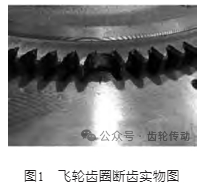
二、原因分析
飛輪齒圈的材料為45號鋼,供應商的制造工藝流程如圖2所示。為查找齒圈斷齒原因,采用二分法進行FTA,如圖3所示。
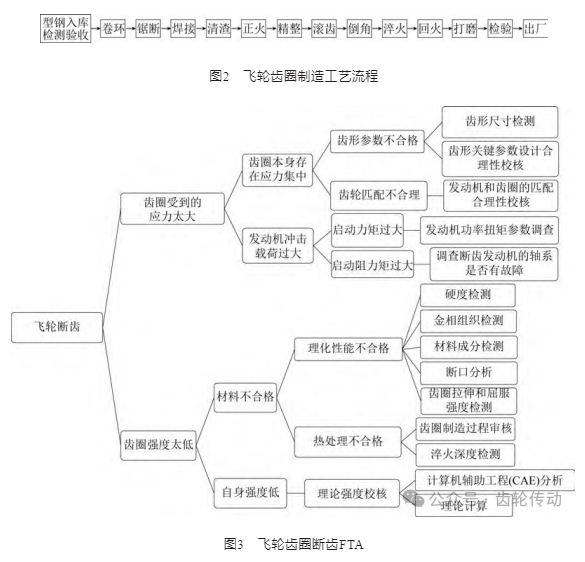
通過FTA可系統梳理可能導致斷齒的各類因素及其邏輯關系,有助于針對性實施相應改進措施,從根源上徹底解決飛輪齒圈斷齒問題,進而保障發動機正常運行。
通過實施飛輪齒圈齒形檢測、發動機與齒圈匹配評估、發動機功能功率扭矩參數調研,以及故障發動機軸系檢查等一系列工作,排除齒圈本身存在應力集中和發動機沖擊載荷過大,致使齒圈受異常外力而斷齒的可能。為深入查明斷齒原因,本研究進一步從故障齒圈的材料理化性能、熱處理和理論強度校核等方面進行排查。
齒圈理化性能檢測
對2個故障齒圈材料成分進行檢測,飛輪齒圈故障件化學成分見表1。由表1可以看出:各種元素的材料成分均符合45號鋼的標準要求。

飛輪齒圈齒頂需進行淬火處理以保證有足夠硬度與發動機小齒輪嚙合,要求淬火后齒面洛氏硬度為50~55 HRC。對故障飛輪齒圈硬度進行檢測,結果見表2。

由表2可以看出:飛輪齒圈故障件的硬度檢測結果均滿足要求。齒圈硬化層分布對飛輪齒圈的使用壽命至關重要,飛輪齒圈淬火硬化時需淬透齒面且齒根要有一定硬化深度。若齒根未被有效硬化,則齒面淬透處會產生殘余壓應力,齒根產生殘余拉應力,這個殘余拉應力會明顯降低齒根處的彎曲疲勞強度,從而降低齒圈的使用壽命。當硬化層沿齒面分布(齒根未硬化)時,齒輪的彎曲疲勞強度僅為硬化層沿齒廓分布(齒根硬化)時的50%左右。根據 JB 4187—1986 《汽車發動機飛輪齒圈技術條件》,齒槽底部硬化層深度不應小于0. 5 mm。為保證淬火有效性,淬火硬化層深度要超過飛輪齒圈齒根0. 5~3. 0 mm 。由表2可知,雖然淬硬層沿齒面均勻分布,但是齒根處硬化深度不達標,發生斷齒的2. 8 L發動機飛輪齒圈淬硬層深度未覆蓋至齒槽以下,故不符合設計標準。綜上,該失效飛輪齒圈沿齒根整齒折斷與齒根硬化深度不夠進而導致齒圈彎曲疲勞強度不足存在因果關系。
齒根是齒輪結構設計的薄弱環節,過渡圓角曲率半徑大小直接影響齒根應力集中程度,過渡圓角越小,應力集中程度越強。按照GB/T 1356—2001《通用機械和重型機械用圓柱 齒輪 標準基本齒條齒廓》要求,齒根過渡圓角半徑≥0. 38m(m為齒圈模數,本文齒圈模數為2. 75)。2. 8 L發動機飛輪齒圈的齒根過渡圓角設計值為1. 0~1. 5 mm,基本符合設計標準要求(≥1. 045 mm)。
斷口分析
對故障齒圈進行斷口分析,并查找失效原因,結果如圖4所示。由圖4(a)可知:斷口于齒根處斷裂,由一側向另一側呈剪切斷裂,斷口左右兩側存在顯著的剪切滑移痕跡,斷口中心呈反光小刻面特征。該宏觀形貌屬于典型的兩邊韌性斷裂、中間脆性斷裂。由圖4(b)和圖4(c)可知:起斷區呈現韌窩形貌,且未發現夾雜等缺陷;中間區域為韌窩形貌,韌窩為拉長韌窩,與斷裂方向平行;止斷區形貌與中間區域形貌一致,整體形貌表現為材料拉伸滑移,且滑移方向與應力方向一致。
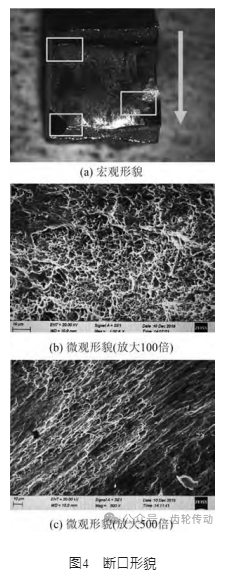
有限元分析
起動機齒輪材料為20CrMnTi,飛輪齒圈材料為 45號鋼,材料參數見表3。對飛輪齒圈進行有限元分析,模型截取飛輪齒圈和發動機齒輪數模,導入Ansys Workbench進行網格劃分,對接觸齒輪嚙合部分進行局部網格細化(網格尺寸為0. 2 mm),劃分好的有限元模型如圖5所示。
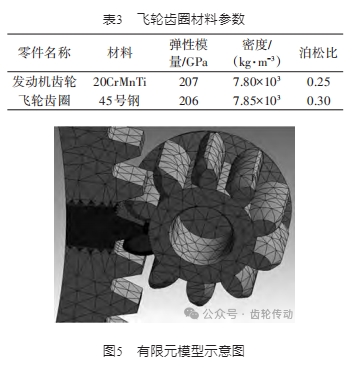
在 Ansys Workbench 中根據表 3 賦予相應材料后,將齒輪嚙合面設置摩擦接觸,摩擦因數為0. 15;約束飛輪齒圈內圓所有自由度;放開發動機齒輪軸繞軸線的旋轉自由度,同時約束其他方向自由度;在發動機驅動齒輪(小齒輪)上加載12 N·m扭矩,查看飛輪齒圈應力變化情況,結果如圖6所示。
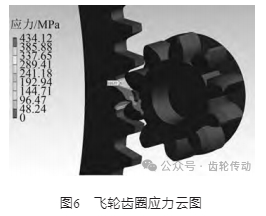
由圖6可知:靜態條件下,飛輪齒圈齒根處最大綜合米塞斯應力為165. 77 MPa;而在動載條件下,齒圈根部過渡圓角處的最大彎曲應力為681 MPa。飛輪齒圈材料為45號鋼,根據GB/T 1172—1999《黑色金屬硬度及強度換算值》可得:淬火后的 45 號鋼抗拉強度(1 710 MPa)>齒根圓角彎曲應力(681 MPa)>非淬火 45 號鋼抗拉強度(600 MPa)。從上述分析可知,如果飛輪齒圈存在未淬透的齒根,如遇較大動載時,便會存在斷裂風險。
三、改進措施
結合理化性能檢測、斷口分析和有限元分析結果,失效齒圈沿齒根整齒折斷,與齒根無硬化層而導致的彎曲疲勞強度不足有直接關系。為此提出改進措施:① 將齒圈淬火深度加深至齒根圓以下1~ 2 mm;② 齒根過渡圓角半徑從原來的1. 0~1. 5 mm 加嚴至1. 3~1. 5 mm。隨后將上述2項改進建議通過圖紙予以固化,并下發供應商嚴格執行。圖 7(a)為改進后的飛輪齒圈,經檢測其齒根淬硬層厚度為1. 7 mm,齒面淬硬層深度為 7. 8 mm;圖 7(b)、(c)為抽檢改進后飛輪齒圈的金相組織檢測云圖,其中淬硬層為馬氏體組織,過渡區為回火馬氏體+屈氏體+鐵素體。為進一步驗證改進效果,對齒圈開展齒向疲勞試驗和齒沖擊試驗。試驗結果表明,改進后的飛輪齒圈未出現裂紋和斷裂,各項指標均合格。
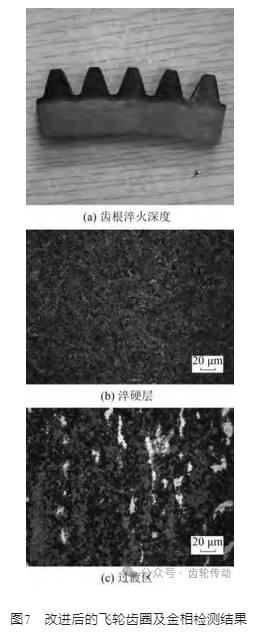
通過市場反饋信息可知,改進后的飛輪齒圈在實際使用中未再發生斷齒情況。
四、結語
在飛輪齒圈的設計過程中,除滿足相應的嚙合要求及材料性能要求外,一些影響齒圈性能的關鍵參數和尺寸需固化到圖紙上,供應商在齒圈制作過程中需嚴格按照圖紙執行生產。同時,在設計過程中還需考慮飛輪齒圈實際受力情況,及時對飛輪齒圈進行全面分析及驗證。
本文針對 2. 8 L發動機飛輪齒圈頻繁出現斷齒故障展開研究。通過對故障現象的觀察,發現斷齒發動機行駛里程短,屬于早期失效,且飛輪齒圈特定齒位呈現斷裂與磨損特征。運用FTA法系統梳理導致斷齒的因素,經一系列排查后,從齒圈理化性能、斷口、有限元分析等方面進行深入探究,結果如下:理化性能檢測表明,材料成分符合標準,但齒根硬化深度不達標;斷口分析顯示為兩邊韌性斷裂、中間脆性斷裂特征;有限元分析得出齒根處應力情況,揭示未淬透齒根遇較大動載存在斷裂風險。為此,采取將齒圈淬火深度加深至齒根圓以下 及加嚴齒根過渡圓角半徑的改進措施。改進后的齒圈經檢測與試驗,各項指標合格,再未出現斷齒情況。
作者簡介:辛雪軍(1984—),男,碩士,工程師,主要研究方向為整車與發動機結構強度及NVH分析。
參考文獻略.