齒輪冷擺輾精密成形是通過錐形擺頭繞自身軸線自轉-繞設備軸線公轉合成的回轉搖擺運動和凹模直線進給運動使工件產生連續局部塑性變形累積整體成形的先進成形技術, 具有成形力小、充模效果好、生產效率高等優點, 可以成形閉式冷精鍛無法成形的大模數大直徑齒輪。
武漢理工大學華林團隊自 20 世紀 90 年代以來, 針對圓錐直齒輪冷擺輾機理、冷擺輾成形規律、產品檢測和質量控制、冷擺輾齒輪坯料預處理及長壽命模具設計制造等進行了系統深入研究。闡明了圓錐直齒輪擺輾成形-滲碳淬火宏觀精度和微觀組織演變規律, 確定了齒輪擺輾成形極限, 建立了齒輪冷擺輾成形理論, 發明了高性能齒輪齒形無切削冷擺輾成形方法, 攻克了模具-電極-預應力圈設計制造、擺輾-滲碳淬火測控關鍵技術, 冷擺輾成形齒輪晶粒細化、流線連續分布, 精度 6 ~ 7 級, 取消齒形磨削加工, 提高疲勞壽命 1 ~ 2 倍, 提高生產率 10~20 倍, 在我國首次實現了高精度乘用車齒輪無切削冷擺輾精密成形制造和規?;a, 并獲得 2005 國家科技進步二等獎, 這也是我國齒輪精密塑性成形技術首次獲得國家科技進步獎。
根據圓錐直齒輪結構特點和擺輾設備運動方式, 圓錐直齒輪冷擺輾成形過程如圖 10 所示。圓錐直齒輪的齒形分布在錐面上且齒形輪廓為直線, 將擺頭設計為回轉的錐面, 下模為齒形型腔, 擺輾成形時, 在擺頭擺動和齒形下模進給運動的協同往復作用下, 齒坯發生塑性變形填充齒形型腔, 逐漸成形齒輪。由于圓錐直齒輪冷擺輾成形過程是坯料在復雜模具運動作用下發生的局部塑性變形, 且變形區從上往下依次傳遞, 因此需要從理論上解決圓錐直齒輪穩定成形關鍵技術問題。本團隊根據圓錐直齒輪擺輾成形工藝特點, 通過幾何學、運動學和塑性力學研究, 結合有限元建模仿真分析, 提出了圓錐直齒輪冷擺輾成形條件, 揭示了圓錐直齒輪冷擺輾變形規律、力能參數變化特點和微觀組織分布規律。
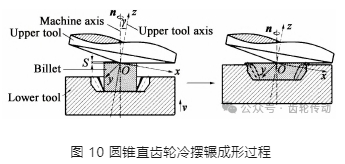
1.圓錐直齒輪冷擺輾精密成形條件
(1) 穩定擺動輾壓條件
為了實現圓錐直齒輪連續且穩定地輾壓成形, 齒坯需要在擺輾成形過程中始終與下模保持相對靜止, 即必須保證作用于齒坯局部變形區水平方向拖曳力小于齒坯靜摩擦力, 且齒坯在下模進給方向受力必須平衡, 因此, 根據圓錐直齒輪冷擺輾成形穩定輾壓力學模型、庫倫摩擦條件和幾何運動關系可得到圓錐直齒輪冷擺輾成形穩定輾壓條件, 如式 (2) 所示。

式中: s 為下模每轉進給量; R0 為齒坯初始半徑; γ 為擺頭擺角; μ1、μ2 分別為擺頭與齒坯上表面和下模與齒坯下表面摩擦因數。
(2) 塑性鍛透條件
圓錐直齒輪冷擺輾成形穩定輾壓條件是齒輪擺輾變形的必要條件, 但并不能保證整個齒坯發生塑性變形而成形出形狀較好的齒形。在圓錐直齒輪冷擺輾成形過程中, 塑性變形區的形狀和大小對齒輪變形均勻性、金屬材料流動和力能參數有重要的影響。而塑性變形區是由擺頭局部接觸齒坯上表面發生塑性變形而產生的, 隨著時間的變化而變化, 因此為了保證成形齒形精度, 必須保證塑性變形區從坯料上表面穿透到整個齒坯高度才能實現齒坯高度減小齒形形成的塑性變形, 即需要滿足鍛透力學條件。根據圓錐直齒輪冷擺輾成形塑性變形區變化特點、滑移線場理論等, 可推導出圓錐直齒輪冷擺輾成形塑性鍛透條件, 如式 (3) 所示。

式中: H0 為初始高度; v 為下模進給速度; t 為擺輾成形時間。
在給定坯料尺寸、擺頭擺角和下模進給速度條件下, 為了保證圓錐直齒輪冷擺輾成形過程中連續穩定地輾壓成形且成形出形狀較好的齒形, 下模每轉進給量可以根據式 (2) 和式 (3) 來確定。
2.圓錐直齒輪冷擺輾變形規律
(1) 有限元模型
基于圓錐直齒輪成形規律和生產組織, 提出了圓錐直齒輪冷擺預成形+冷擺輾終成形的兩步成形工藝。根據冷擺輾模具型腔設計、電極設計和成形鍛件之間的關系確定了兩步成形工藝中的預鍛件圖和終鍛件圖。為了保證成形齒輪的質量, 將成形模擬過程分為齒形填充和表面精整兩個階段, 根據圓錐直齒輪冷擺輾穩定成形條件和鍛透條件, 給出了模擬過程擺頭轉速與凹模進給速度的設計方案和齒坯設計方案, 利用剛塑性原理建立了兩步擺輾成形工藝有限元模型, 如圖 11 所示。
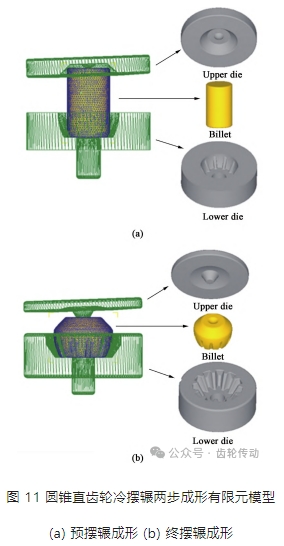
(2) 幾何形狀演變特點
圓錐直齒輪兩步冷擺輾形狀演變如圖 12 所示。在擺輾預成形初期, 擺頭與齒坯上表面先發生接觸, 接觸區材料先發生變形, 在擺頭擺動和凹模進給運動的作用下, 工件高度減小、工件上表面直徑略微增加同時凹模與毛坯的下側面發生接觸, 該區域金屬開始發生塑性變形; 由于擺頭周期性擺動, 靠近擺頭的金屬流動速度比靠近凹模的金屬流動速度要大得多, 從而呈現出 “蘑菇形” 效應。隨著擺輾終成形過程的繼續, 齒坯進入穩定成形階段, 齒形輪廓逐漸成形, 并逐漸向大端擴展, 且大端齒形先充滿, 而且在大端齒形之間開始形成飛邊, 在成形的最后階段, 由于金屬徑向流動阻力急劇增大, 迫使多余金屬向齒形小端流動從而成形小端齒形。
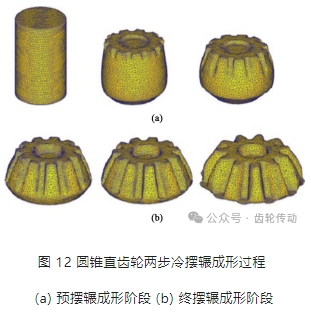
(3) 成形材料流動特點
圖 13 為圓錐直齒輪兩步冷擺輾成形過程中金屬流動速度場分布特點。由于擺輾成形是擺頭與坯料局部接觸施加載荷使金屬發生塑性變形, 因此在預擺輾成形和終擺輾成形過程中, 工件變形區可分為與擺頭接觸的主動變形區及未與擺頭接觸的被動變形區。在預擺輾成形階段, 主動變形區金屬在擺頭和凹模共同作用下主要沿坯料徑向流動, 是坯料發生塑性變形的主要動力。被動變形區的金屬未受 到擺頭的直接作用, 而是在凹模向上擠壓的同時受到主動變形區的牽連作用下而發生微弱的背離下形腔的運動, 而且主動變形區的金屬流動速度明顯大于被動變形區的金屬流速。
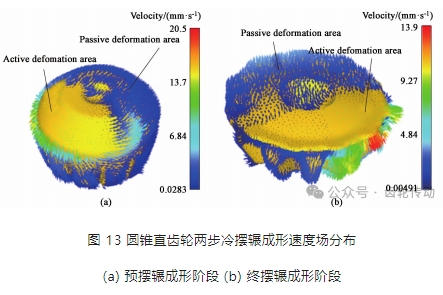
(4) 成形力能參數變化規律
圖 14 所示為圓錐直齒輪兩步冷擺輾成形過程中軸向載荷-時間曲線。分析發現, 在預擺輾成形和終擺輾成形過程中, 軸向載荷變化特點均可分為 4 個階段。在預擺輾成形過程中, 第 1 階段擺頭中部的凸臺與坯料接觸, 接觸區域金屬發生塑性變形, 因此軸向載荷迅速從零增加到某一值; 隨著變形的進行, 擺頭逐漸接觸坯料的整個上端面, 軸向載荷急劇增大至相應的數值, 即第 2 階段; 第 3 階段坯料到達了齒形填充階段, 軸向載荷先緩慢增加, 隨后迅速達到峰值。在預擺輾成形最后階段, 凹模停止了軸向進給, 導致軸向成形力迅速降低。終擺輾成形與預擺輾成形不同之處是在第 3 階段 (齒形完整充填型腔階段), 前者的金屬流動阻力更大, 軸向載荷迅速增加到峰值, 其峰值載荷遠高于預擺輾成形階段峰值載荷。
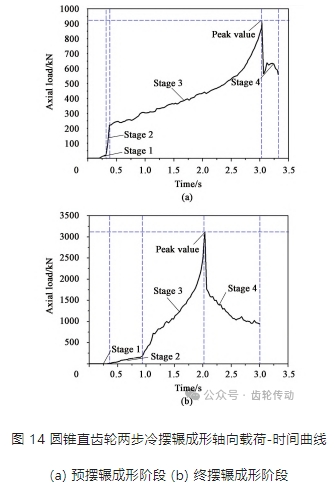
(5) 微觀組織演變規律
為了研究圓錐直齒輪擺輾成形-滲碳淬火微觀組織演化規律, 以等溫球化退火的 20CrMnTi 齒輪鋼為坯料實驗材料, MoS2 為潤滑劑, 按照棒坯-預擺輾成形-退火-終擺輾成形進行實驗, 得到冷擺輾成形圓錐直齒輪, 然后對齒輪沿不同方向不同位置截取試樣進行金相分析和硬度測試, 得到圓錐齒輪冷擺輾成形微觀組織分布特點, 如圖 15 所示。研究發現: 齒廓部位的晶粒發生顯著變形, 晶粒被拉長, 原始組織中的少量片狀珠光體也因塑性變形而破碎, 形成沿變形方向分布的顆粒狀碳化物; 從齒頂表面到齒根表面的晶粒的變形程度逐漸增大, 特別是齒根表面晶粒已經呈明顯的纖維狀; 心部的晶粒形狀基本不發生變化, 僅鐵素體晶界上聚集分布著顆粒狀碳化物, 局部晶界處的碳化物分布較為密集。冷擺輾變形后, 齒廓處為分布均勻的等軸細小晶粒, 其大小約為 15 μm。在距齒廓 400 ~ 900 μm 處, 晶粒更加細小, 約為 10 μm 左右。
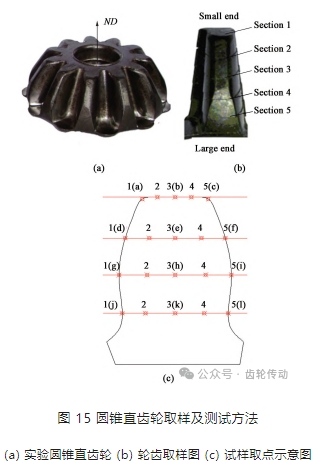
利用蔡司 ULTRA PLUS-43-13 場發射掃描電子顯微鏡對齒頂、分度圓和齒根處進行了 DBSD 分析, 得到了齒輪表面織構分布特點, 如圖 16 所示。分析發現: 隨著變形量的增加, 沿晶粒拉長方向大角度晶界的間距減小。當到達齒廓時, 大角度晶界的間距非常小, 晶界幾乎平行于 RD 方向。經過冷擺輾后, 輪齒表面的金屬受不同程度的塑性變形, 織構發生明顯的變化。齒頂處織構方向性并不明顯, 但在分度圓處織構形成了很強的方向性, 占主導地位的織構組分為 {112} < 110 >和 {110}<112>; 當變形量達到最大時, 齒根處織構的方向性更強, 占主導地位的織構組分為 {112} <110> 和 {111}<110>。
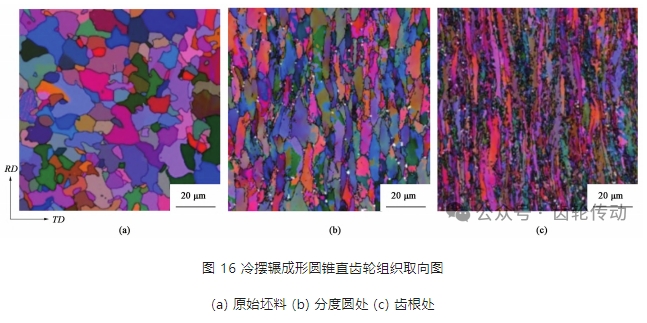
齒輪復合精鍛成形技術
21 世紀以來, 汽車輕量化電動化發展要求精密塑性成形制造更高精度、更大模數和尺寸的高性能齒輪。為此, 武漢理工大學、華中科技大學與江蘇太平洋精鍛科技公司等合作, 綜合了冷精鍛、熱精鍛和局部變形整體成形優點, 將齒輪冷擺輾技術擴展到熱精鍛+冷擺輾等齒輪復合精密成形技術, 并開發了系列齒輪精密成形自動化產線, 批量精密成形制造新能源乘用車圓錐直齒輪、圓柱直齒輪、結合齒輪等。齒輪復合精鍛成形技術是將冷、熱精鍛工藝進行組合完成齒輪的精密成形鍛造, 充分利用了熱鍛材料塑性好、流動應力低, 齒輪主要變形過程用熱鍛完成; 而冷鍛成形精度髙, 齒形部分主要尺寸形狀用冷精鍛終成形完成, 從而得到高精度高性能的齒輪零件。齒輪復合精鍛技術具有材料利用率高、生產效率高及成形齒輪精度高等優點, 特別適合材料強度高、形狀復雜、成形精度要求高的大模數大尺寸齒輪的成形制造。
近年來, 武漢理工大學華林教授團隊針對航空齒輪材料強度高、難變形及性能要求高等特點, 提出了熱擺輾預成形+冷擺輾精整的復合擺輾成形技術, 主要工藝過程如圖 17 所示。通過建立變形-傳熱耦合的剛粘塑性有限元模型分析優化了航空齒輪復合擺輾成形過程, 并進行了熱-冷擺輾復合成形工藝實驗, 如圖 18 所示。
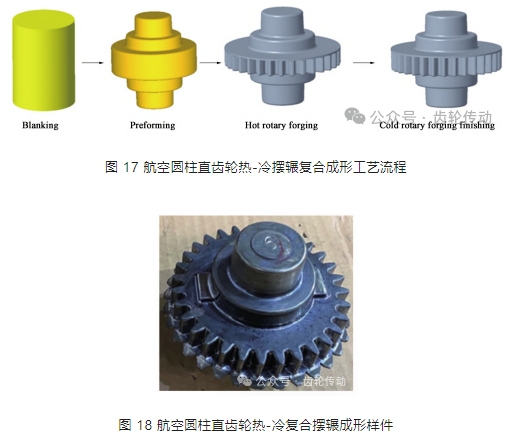
三、齒輪精密成形裝備與產線
齒輪成形裝備與產線是實現齒輪精密塑性成形制造的關鍵。為了滿足齒輪成形制造的高精度、高效率、綠色化和智能化, 齒輪成形裝備應具有較好的剛性、精密的導向機構、多向協同運動能力、生產工序的自動監控和自動檢測等特點。齒輪冷精鍛成形的主要工藝流程為: 下料→ 球化退火→ 磷皂化→ 預成形→ 退火 →磷皂化→ 冷精鍛終成形→ 切飛邊 →熱處理 →檢驗等。齒輪熱精鍛成形的主要工藝流程為: 下料 →加熱→ 潤滑→ 制坯 →預鍛熱成形→ 熱精鍛終成形→ 切飛邊 →熱處理 →檢驗等。齒輪復合精鍛成形的主要工藝流程為: 下料→ 加熱→ 潤滑 →制坯 →熱鍛/溫鍛成形 →切飛邊→ 熱處理→ 冷精鍛→ 熱處理 →檢驗等。表 2 為齒輪精密成形各工藝流程所用設備。
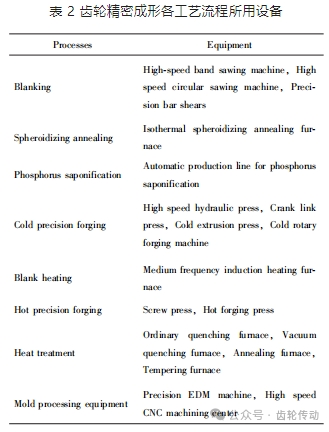
齒輪熱精鍛成形常用的設備有高能螺旋壓力機、熱模鍛壓力機和離合器式螺旋壓力機等。齒輪冷精鍛成形常用的設備有冷鍛壓力機、冷擠壓機和冷擺輾機等。熱模鍛機械壓力機通常采用偏心軸、曲軸連桿、楔式和肘桿機構。冷鍛壓力機與熱模鍛壓力機結構類似, 但剛性、速度和偏載能力與熱模鍛壓力機不同。模鍛液壓機是利用油或水作為動力介質, 有三梁四柱或者框架結構。小型模鍛液壓機可用于精密齒輪鍛造、擠壓或者復合成形工藝。冷擺輾機主要有瑞士 Schmid 公司生產的 T200 和 T630 型, 適合直徑為 Φ200 mm 左右的齒輪冷擺輾精密成形, 但其造價太高。為了降低冷擺輾機造價, 國內一些研究院所和工廠相繼設計研究了多種規格擺輾機, 但精密成形穩定性不夠。
近年來, 武漢理工大學華林教授團隊基于冷擺輾幾何學、運動學和成形力學規律, 發明了冷擺輾機新型運動軌跡, 提出了多軌跡、小振動高性能齒輪新型冷擺輾機設計方法, 研制了 300T 冷擺輾成形裝備。在此基礎上, 進一步消除單錐輥擺輾機偏心加載缺點, 研制了國際首臺 500T 雙錐輥擺輾機, 實現了薄腹板齒輪平衡加載成形, 相關設備如圖 19 所示。
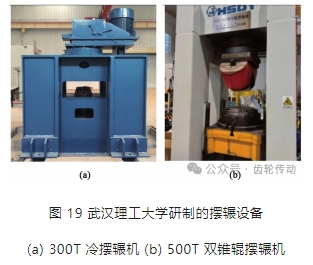
為了進一步提高齒輪精密成形效率和質量, 許多企業相繼開發和應用了多工位齒輪熱精鍛/ 冷精鍛自動化產線, 正在向著齒輪精密成形智能自動化方向發展。目前江蘇太平洋精鍛公司已經建設多條齒輪精密成形自動化生產產線, 該公司的某條 C2F-25 圓錐直齒輪自動化精鍛線可實現毛坯自動上料-坯料自動化中頻感應加熱-毛坯自動進料到工位-多工位自動鍛造和搬運-自動模具冷卻潤滑-自動快速換模-自動裝框等多工位熱精鍛自動化生產, 顯著提高了齒輪生產效率、模具壽命和產品精度。
四、齒輪精密成形技術應用
隨著節能與新能源汽車國際競爭日益加劇, 要求汽車傳動齒輪重量輕、強度高、精度高、成本低, 具有節省材料能源、降低生產成本、提高產品精度和生產效率的齒輪精密成形技術應用發展更加快速。精度要求不高的商用車齒輪廣泛應用熱精鍛成形技術, 精度要求高的乘用車齒輪廣泛應用冷精鍛成形技術、熱精鍛-冷精鍛復合成形技術。
齒輪無切削熱精鍛成形
商用車、拖拉機和工程機械等差速器圓錐直齒輪精度 9~ 10 級, 目前已廣泛應用齒形無切削熱精鍛成形生產。汽車工業發達的德國、日本和美國等國家自 20 世紀 60 年代以來, 逐步實現了商用車差速器圓錐直齒輪無切削精密熱鍛成形批量生產。我國自 20 世紀 80 年代以來, 逐步實現了商用車差速器圓錐直齒輪無切削精密熱鍛成形批量生產。熱精鍛設備主要有摩擦壓力機、電動螺旋壓力機、機械壓力機、液壓機等, 熱精鍛成形齒輪模數 2~12, 直徑 Φ300 mm 左右。
齒輪無切削冷精鍛成形
乘用車齒輪精度為 6~ 7 級, 熱精鍛成形不能滿足精度要求。20 世紀 90 年代武漢理工大學開發了圓錐直齒輪冷擺輾精密成形技術, 實現了齒形無切削成形制造。先后與湖北車橋公司、江蘇太平洋精鍛公司等合作, 建設了乘用車圓錐直齒輪無切削冷擺輾精密成形產線, 率先實現了我國高精度乘用車齒輪無切削冷擺輾精密成形規?;a。齒輪冷擺輾連續局部變形, 抗力小、精度高、金屬流線連續、晶粒組織細化, 大幅提高了齒輪疲勞性能和使用壽命, 使我國汽車齒輪技術經濟水平進入國際先進行列。在齒輪冷擺輾精密成形技術和產線基礎上, 武漢理工大學、華中科技大學與江蘇太平洋精鍛科技公司等合作, 進一步開發了冷精鍛、冷擠壓、熱精鍛+冷精鍛/冷擺輾等齒輪復合精密成形技術與產線, 實現了節能與新能源汽車變速器齒輪、同步器齒環、差速器齒輪等系列齒輪零件規模化生產。冷精密成形齒輪產品不僅廣泛用于一汽、東風、上汽、北汽、廣汽、吉利和比亞迪等我國主流車型, 還與奔馳、寶馬和特斯拉等國際著名車型配套, 顯著提升了我國汽車齒輪零件國際市場競爭力。典型無切削冷精密成形齒輪產品如圖 20 所示。
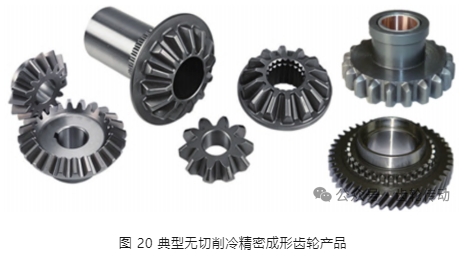
五、齒輪精密成形技術發展
圓錐螺旋齒輪精密成形技術
圓錐螺旋齒輪可以用來傳遞相交軸之間的速度和轉矩, 具有重合度高、承載能力強, 傳動平穩、噪聲小等優點, 是汽車、航空航天裝備重要傳動零件。目前, 國內外齒輪制造企業仍然采用預鍛齒坯+銑齒+磨齒方式生產圓錐螺旋齒輪, 存在加工效率低、材料利用率低、疲勞性能差等問題, 無法滿足汽車、航空航天裝備發展需求。近幾十年來, 雖然國內外研究人員針對圓錐螺旋齒輪精密成形進行了許多探索研究, 但圓錐螺旋齒輪復雜形狀難以充模成形和脫模等問題一直未能解決。近年來, 武漢理工大學華林團隊針對圓錐螺旋齒輪復雜形狀幾何特點, 提出了圓錐螺旋齒輪多自由度包絡成形新方法, 并進行了包絡成形工藝實驗。
基于多自由度包絡成形原理, 對于難成形的圓柱螺旋齒輪、圓錐螺旋齒輪等復雜形狀齒輪, 武漢理工大學研制了國際首臺 800T 六自由度空間包絡成形裝備, 實現了航空圓錐螺旋齒輪、面齒輪等多自由度包絡成形制造。應用該設備成形的航空螺旋錐齒輪、航空面齒輪如圖 21 所示。
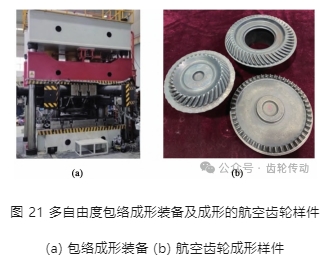
非圓錐直齒輪熱精鍛成形技術
非圓錐直齒輪屬于變速比傳動機構, 能夠執行許多圓錐直齒輪難以執行的特殊傳動模式, 因此非常適合用于具有特種性能需求的傳動裝置。由于非圓錐直齒輪節曲線為空間型曲線, 幾何形狀更為復雜, 各齒上的金屬流動過程存在顯著差異, 因此其成形難度更大。目前, 非圓錐直齒輪主要采用五軸聯動數控加工中心進行加工。根據非圓錐直齒輪結構特點, 武漢理工大學華林團隊開發了下料-加熱-預制坯-終鍛非圓錐直齒輪熱精鍛成形工藝, 提出了通過分割齒區間轉換為具有扇形截面的扇形柱體的思路來建立預制坯精確設計方法, 實現了非圓錐直齒輪熱精鍛成形, 如圖 22 所示。
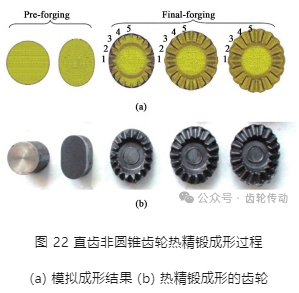
六、結語
齒輪是機械裝備的核心基礎件, 對高端裝備性能及壽命有著重要影響。以高性能航空圓錐螺旋齒輪、面齒輪等完整流線精密成形技術與應用為代表的高端齒輪先進制造技術亟待突破, 我國塑性成形科技工作者面臨著光榮使命。通過產學研密切合作, 一定會使我國高端齒輪精密成形技術與裝備實現自主創新, 走在世界前列。
參考文獻略.