差速器總成是整車(chē)實(shí)現(xiàn)改變動(dòng)力方向和左右輪轉(zhuǎn)速差等功能的重要零件,差速器總成 NVH 好壞對(duì)整車(chē)低速噪音影響很大,所以對(duì)差速器各零件配合尺寸及零件表面處理方式有很高的要求 . 電驅(qū)動(dòng) 總成搭載某兩驅(qū)純電動(dòng)整車(chē)上市后,2022 年 11 月整車(chē)在低速雙扭線工況行駛時(shí),車(chē)內(nèi)有 “嗚嗚” 異響聲 . 人耳最敏感頻率是 200 ~ 800 Hz 之間的聲音,此異響頻率正在其中,易被人耳識(shí)別,使人極不舒服 . 文中對(duì)整車(chē)低速雙扭線工況進(jìn)行主觀駕評(píng)、振動(dòng)及噪音測(cè)試,通過(guò)人員駕評(píng)、故障車(chē)測(cè)試數(shù)據(jù)分析,并識(shí)別到異響發(fā)生在傳動(dòng)系統(tǒng)上,隨后對(duì)激勵(lì)源和傳遞路徑逐級(jí)進(jìn)行分析排查,最后,通過(guò)行星齒輪表面磷化的優(yōu)化改進(jìn),快速有效地解決困擾該車(chē)型的差速器嗚嗚異響問(wèn)題.
一、故障現(xiàn)象描述
某搭載電驅(qū)動(dòng)總成的兩驅(qū)純電動(dòng)汽車(chē),在低速雙扭線工況加速行駛過(guò)程中,在整車(chē)左或右轉(zhuǎn)彎加油門(mén)時(shí),車(chē)內(nèi)人員都能聽(tīng)到明顯的 “嗚嗚”異響聲,但在此過(guò)程整車(chē)并未出現(xiàn)竄動(dòng),整車(chē)在直行加減速或滑行都無(wú)此異響聲 . 整車(chē)低速雙扭線工況行駛時(shí),這種金屬摩擦聲易被車(chē)內(nèi)人員聽(tīng)到,并產(chǎn)生極大抱怨 . 為了快速識(shí)別產(chǎn)生 “嗚嗚”異響的故障源,把故障車(chē)上舉升機(jī),模擬整車(chē)雙扭線工況,異響未復(fù)現(xiàn). 通過(guò)對(duì)整車(chē)底盤(pán)結(jié)構(gòu)分析,初步確定故障與轉(zhuǎn)向差速時(shí)關(guān)聯(lián)件有關(guān),須對(duì)左右半軸、差速器等關(guān)聯(lián)件進(jìn)行振動(dòng)響應(yīng)噪音測(cè)試.
二、故障現(xiàn)象確認(rèn)
對(duì)故障車(chē)進(jìn)行測(cè)試
1) 在整車(chē)半軸支架、中間軸軸承及差速器軸承殼體處布置傳感器測(cè)試,如圖 1,整車(chē)雙扭線行駛軌跡,如圖 2.
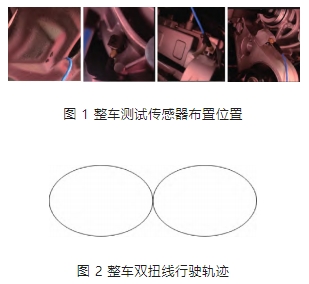
2) 整車(chē)測(cè)試數(shù)據(jù)分析結(jié)果,如圖 3 和圖 4.
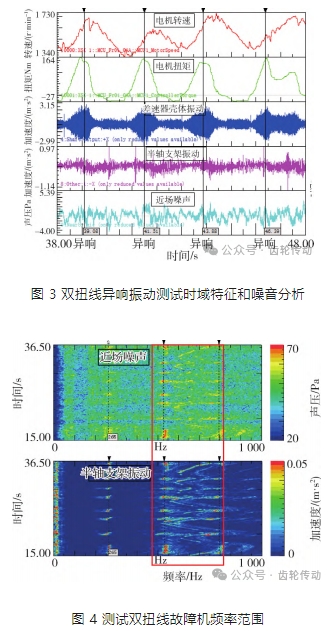
通過(guò)對(duì)整車(chē)左右半軸支架、差速器軸承處殼體和中間軸軸承處殼體位置布點(diǎn)測(cè)量其振動(dòng)和噪音信號(hào)并分析時(shí)域特征和音頻數(shù)據(jù),差速器殼體振動(dòng)加速度出現(xiàn) 5 次的瞬時(shí)沖擊特征,其振動(dòng)沖擊最大,超過(guò)半軸底盤(pán)件的 3 倍,
差速器軸承處殼體附近的振動(dòng)是傳動(dòng)旋轉(zhuǎn)件非線性規(guī)律的信號(hào),同時(shí) “嗚嗚”異響噪聲主要頻率在 500 ~ 1 000 Hz 之間,而非在半軸頻率的 200 ~ 300 Hz 之間,結(jié)合主觀駕評(píng)可以初步鎖定此 “嗚嗚”異響來(lái)源電驅(qū)動(dòng)差速器總成異響.
三、故障原因分析排查
整車(chē)低速雙扭線差速器異響影響因子識(shí)別
通過(guò)對(duì)差速器嗚嗚異響故障產(chǎn)生的機(jī)理分析,識(shí)別出差速器異響因子,如圖 5.
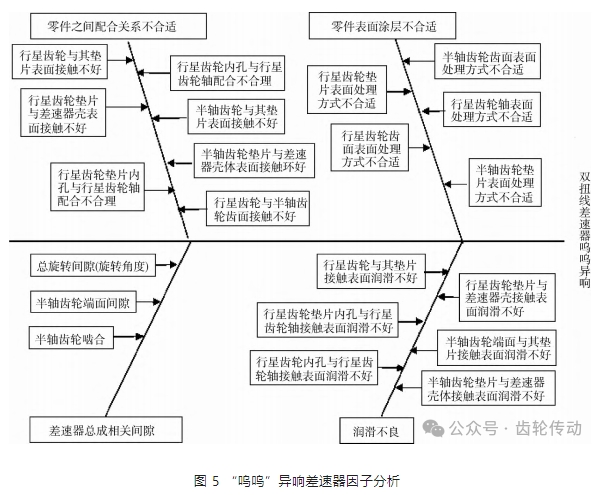
差速器內(nèi)部結(jié)構(gòu)設(shè)計(jì)簡(jiǎn)述
差速器總成結(jié)構(gòu)爆炸圖如圖 6,其零部件有差速器殼體空腔內(nèi)分布左右半軸齒輪墊片及半軸齒輪,上下分布行星齒輪墊片及行星齒輪,裝配時(shí),把左右半軸齒輪墊片及半軸齒輪、上下分布行星齒輪墊片及行星齒輪,放在差速器殼體內(nèi),行星齒輪軸穿過(guò)差速器差殼、行星齒輪及行星齒輪墊片的內(nèi)孔,再通過(guò)卷銷(xiāo)固定到差速器殼體上,把主減齒輪壓裝到差速器殼體上并焊接,再對(duì)主減齒輪進(jìn)行磨齒,通過(guò)兩端軸承分別位于差速器殼體左右兩端軸頸,裝配到殼體軸承孔內(nèi),起到支撐作用 .
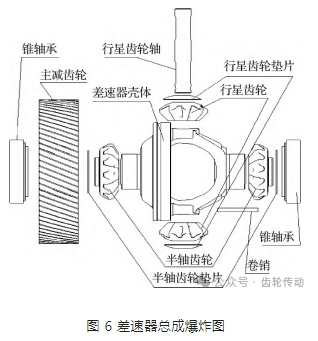
整車(chē)差速工況及行星齒輪自轉(zhuǎn)關(guān)聯(lián)計(jì)算
整車(chē)低速雙扭線工況行駛時(shí),由于兩側(cè)車(chē)輪轉(zhuǎn)彎半徑的差異,差速器的內(nèi)摩擦力矩引起兩個(gè)行星齒輪方向相反的自轉(zhuǎn)運(yùn)動(dòng),以抵消車(chē)輪之間的轉(zhuǎn)彎附加阻力矩,如圖 7 所示 . 行星齒輪驅(qū)動(dòng)半軸之間的轉(zhuǎn)速差 Δω 為

式中: ω1 為外側(cè)半軸轉(zhuǎn)速; ω2 為內(nèi)側(cè)半軸轉(zhuǎn)速; ω3 為行星齒輪自轉(zhuǎn)轉(zhuǎn)速; z1 為行星齒輪齒數(shù),齒數(shù)為 9; z2 為半軸齒輪齒數(shù),齒數(shù)為 13
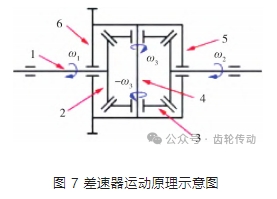
根據(jù)采集整車(chē)雙扭線異響工況測(cè)試數(shù)據(jù),通過(guò)式 (1) 計(jì)算出行星齒輪的自轉(zhuǎn)速度,如表 1.
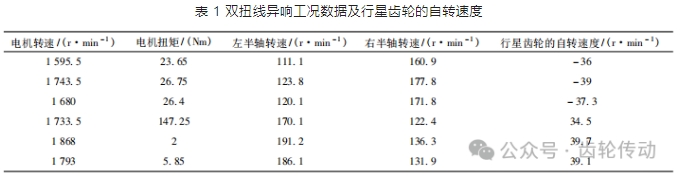
客退件總成臺(tái)架故障復(fù)現(xiàn)測(cè)試
把客退有 “嗚嗚”異響的電驅(qū)動(dòng)總成,按照整車(chē)異響工況上臺(tái)架進(jìn)行復(fù)測(cè),發(fā)現(xiàn)近場(chǎng)噪音和差速器附件殼體振動(dòng)明顯異常,進(jìn)一步鎖定異響來(lái)源為差速器總成內(nèi)部零件,故障復(fù)現(xiàn)測(cè)試結(jié)果如圖 8.
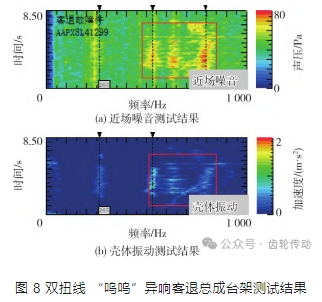
故障件尺寸檢查及關(guān)聯(lián)分析
對(duì)故障件差速總成及零部件尺寸檢測(cè),差速器總成相關(guān)間隙檢測(cè)合格如表 2,再進(jìn)行差速器總成拆解并進(jìn)行零部件尺寸檢測(cè),尺寸合格如表 2,檢測(cè)結(jié)果可排除故障不是零件制造加工問(wèn)題.
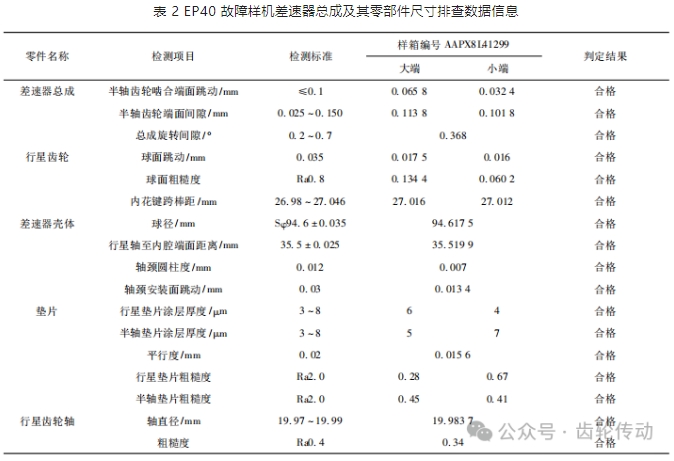
四、對(duì)策制定及驗(yàn)證
通過(guò)對(duì)整車(chē)、電驅(qū)動(dòng)總成臺(tái)架測(cè)試以及差速器內(nèi)部零件結(jié)構(gòu)及工作原理分析,整車(chē)在雙扭線工況行駛時(shí),行星齒輪與行星齒輪軸之間配合間隙較小,在差速器實(shí)現(xiàn)差速時(shí),它們受載出現(xiàn)軸向和自轉(zhuǎn)運(yùn)動(dòng),導(dǎo)致行星齒輪軸與行星齒輪內(nèi)孔發(fā)生不連續(xù)的金屬摩擦聲; 另外行星齒輪內(nèi)孔表面未采用涂層處理和行星齒輪軸表面采用鍍鎳處理,零件表面油膜吸附能力較低,形成地動(dòng)態(tài)油膜較少,同時(shí)在 整車(chē)差速時(shí),它們之間潤(rùn)滑油膜穩(wěn)定性的動(dòng)態(tài)壓力遭到破壞,造成它們發(fā)生干摩擦,最終造成金屬摩擦聲,故通過(guò)上面異響產(chǎn)生的機(jī)理分析,制定以下驗(yàn)證優(yōu)化方案.
雙扭線嗚嗚異響制定對(duì)策
1) 增加潤(rùn)滑油量,同時(shí)適當(dāng)增加行星齒輪軸和行星齒輪內(nèi)孔配合間隙,整車(chē)差速時(shí),它們之間潤(rùn)滑油膜增加,減弱它們之間的金屬摩擦聲;
2) 增加墊片耐磨性,如墊片表面進(jìn)行 MoS2 涂層;
3) 行星齒輪采用磷化處理,增加其內(nèi)孔表面油膜吸附能力,改善其與行星齒輪軸摩擦聲音,摩擦部位如圖 9.
通過(guò)以上優(yōu)化策略,制定組合驗(yàn)證.
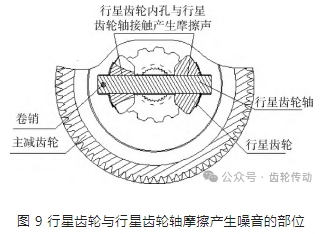
異響對(duì)策方案驗(yàn)證
針對(duì)以上優(yōu)化改善對(duì)策進(jìn)行組合裝配樣機(jī),對(duì)不同方案總成分別進(jìn)行臺(tái)架測(cè)試,測(cè)試驗(yàn)證分析結(jié)果如圖 10 ~ 13.
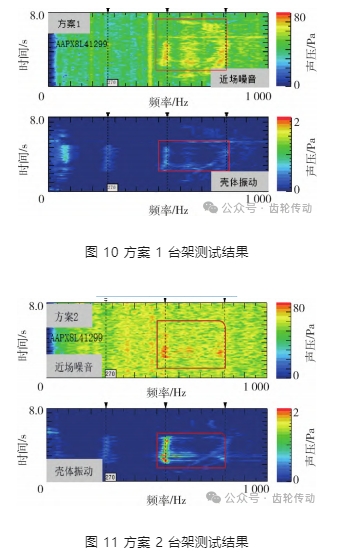
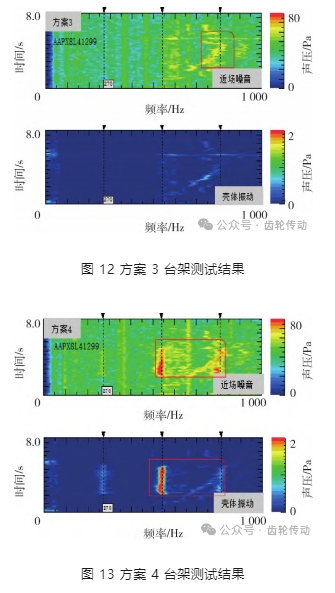
針對(duì)以上優(yōu)化改善對(duì)策,嗚嗚異響驗(yàn)證結(jié)果匯總,下表為 “嗚嗚”異響驗(yàn)證效果如表 3.
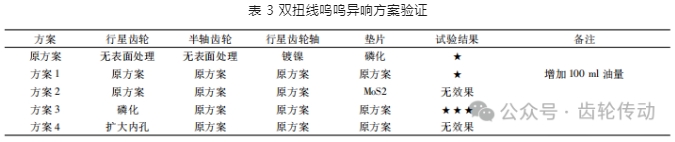
綜上所述,通過(guò)異響產(chǎn)生機(jī)理分析、臺(tái)架及整車(chē)驗(yàn)證結(jié)果,在差速器總成、零部件結(jié)構(gòu)變動(dòng)涉及物料成本及不影響差速器可靠性前提下,從 BOM 成本、加工、裝配工藝、零件變動(dòng)庫(kù)存等經(jīng)濟(jì)角度考慮,文中最終通過(guò)對(duì)行星齒輪表面磷化處理,來(lái)優(yōu)化解決整車(chē)雙扭線差速器異響問(wèn)題,進(jìn)行優(yōu)化件差速器可靠性臺(tái)架試驗(yàn)驗(yàn)證結(jié)果,如圖 14、15 所示.
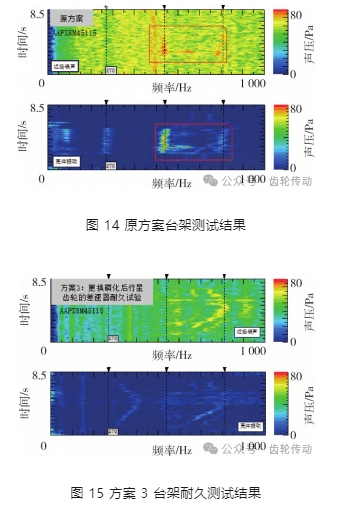
通過(guò)對(duì)客退件行星齒輪磷化處理,進(jìn)行電驅(qū)動(dòng)總成差速可靠性臺(tái)架測(cè)試驗(yàn)證,差速可靠性試驗(yàn)驗(yàn)證,驗(yàn)證時(shí)間相當(dāng)于整車(chē)進(jìn)行 30 萬(wàn)公里行駛里程,雖然試驗(yàn)后仍然有輕微特征,但遠(yuǎn)比故障件特征輕,最總通過(guò)客戶(hù)整車(chē)評(píng)估,目前已按照這種優(yōu)化措施推進(jìn)市場(chǎng)工程化 3 個(gè)多月,整車(chē)投入市場(chǎng)已經(jīng)近萬(wàn)輛,無(wú)一例此問(wèn)題反饋,最終成功攻克此技術(shù)質(zhì)量難題.
五、結(jié)論
純電動(dòng)汽車(chē)噪聲遠(yuǎn)比傳統(tǒng)燃油車(chē)低,整車(chē)雙扭線異響問(wèn)題的影響因素很多,產(chǎn)生異響原因可能各不相同,排查驗(yàn)證周期長(zhǎng),解決問(wèn)題慢的問(wèn)題 . 差速器總成是整車(chē)行駛中實(shí)現(xiàn)改變動(dòng)力方向和實(shí)現(xiàn)左右輪的轉(zhuǎn)速差等功能的重要部件 . 文中以搭載某兩驅(qū)純電動(dòng)整車(chē)雙扭線異響解決思路為例,通過(guò)采集整車(chē)異響工況,電驅(qū)動(dòng)總成在臺(tái)架實(shí)現(xiàn)故障復(fù)現(xiàn) . 通過(guò)對(duì)激勵(lì)、傳遞路徑和響應(yīng)的分析,逐條排除了底盤(pán)相關(guān)激勵(lì)和驅(qū)動(dòng)系統(tǒng)相關(guān)激勵(lì),最終鎖定激勵(lì)源為差速器總成內(nèi)部零件金屬摩擦產(chǎn)生,較全面闡述了該異響問(wèn)題故障因子的分析排查過(guò)程,識(shí)別其異響的主要因子,并通過(guò)優(yōu)化行星齒輪表面磷化涂層處理的方式,成功解決問(wèn)題 . 隨著純電動(dòng)汽車(chē)市場(chǎng)占有率越來(lái)越高,客戶(hù)對(duì)汽車(chē) NVH 性能的要求越來(lái)越高,電驅(qū)動(dòng) NVH 性能水平要求也越來(lái)越高,文中成功解決整車(chē)在低速雙扭線行駛過(guò)程中的嗚嗚異響問(wèn)題,為后期純電動(dòng)電驅(qū)產(chǎn)品開(kāi)發(fā)過(guò)程出現(xiàn)類(lèi)似的問(wèn)題提供了一種較全面、系統(tǒng)、快速經(jīng)濟(jì)地解決思路,無(wú)論為差速器總成自研開(kāi)發(fā),還是選型開(kāi)發(fā),對(duì)后期產(chǎn)品工程產(chǎn)業(yè)化都有很好的借鑒作用 .
參考文獻(xiàn)略.