隨著我國汽車工業的快速發展和汽車電動化的發展趨勢,汽車行業對高強度緊固件的需求劇增。緊固件是一種非常重要,使用很廣泛的連接件,應用廣泛。按 GB 3098.1 的規定,將螺栓、螺釘和螺柱的性能等級分為 10 個級別,8.8 級及以上的稱作高強度緊固件,其應用和發展對現代機械的緊湊小型化、輕量化、高性能化及提高結構工程的連接強度起著重要的作用。由于高強度緊固件的 承載能力和使用壽命比中、低強度緊固件高很多,其延遲開裂現象經常出現,具有廣泛性和多發性特點,失效原因主要包括設計、制造、使用等。另由于延遲斷裂的隱蔽性強,事先很難發現,所以其危害性很大,應當引起相關行業關注。
本文針對汽車差速器用高強度螺栓的延遲開裂現象進行了詳細分析,確定了螺栓的斷裂性質,明確了失效的根本原因,提出了有效的預防和改進措施,并闡述了汽車行業關于高強度螺栓延遲開裂問題的理解與認知,結論可供其他行業緊固件設計者和使用者參考和借鑒。
一、斷裂情況介紹
某批次汽車差速器用高強度螺栓材料牌號為 SCM435,制造工序為:下料→鍛造六角頭→滾壓螺紋→熱處理→表面發黑→除氫。成品性能等級要求為 12.9 級,如圖 1 所示,硬度要求為 39~44 HRC(385~435 HV)。裝配后短期內發生多起斷裂失效,部分安裝完畢后自行斷裂脫落,部分排查擰緊時斷裂脫落。斷裂位置均發生在螺栓六角頭根部 R 角處,失效件宏觀形貌如圖 2 所示。

二、試驗結果及分析
斷口宏觀形貌觀察
失效螺栓斷口宏觀形貌如圖 3 所示。圖中箭頭所示為裂紋快速擴展撕裂棱,并呈典型的棘輪狀特征分布。根據撕裂紋路收斂方向判斷裂源位于斷口邊緣表面區域,裂源處未見與斷裂有關的宏觀冶金缺陷和機械損傷痕跡,瞬斷區位于斷口中部。在宏觀體式顯微鏡下觀察,斷面粗糙,呈結晶顆粒狀,斷面干凈,無腐蝕產物,無明顯宏觀塑性變形,斷面呈典型的脆性斷裂特征,如圖 4 所示。
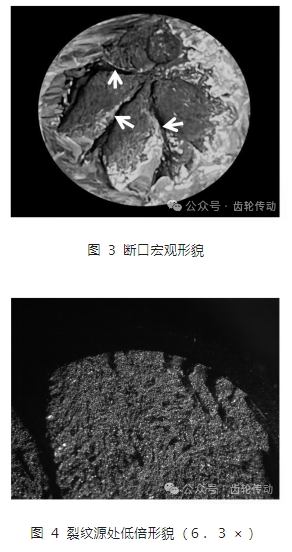
斷口電鏡形貌分析
將螺栓斷口用丙酮超聲波清洗后,在掃描電子顯微鏡下觀察,裂源處未見夾雜、夾渣等冶金缺陷和折疊、擦傷等制造缺陷,斷口呈典型的冰糖狀沿晶斷裂特征,并伴有大量晶間二次裂紋,如圖 5 所示。進一步放大形貌觀察,晶界表面可見明顯塑性撕裂紋路(雞爪紋),如圖 6 所示。心部瞬斷區形貌為韌窩 + 沿晶,如圖 7 所示。
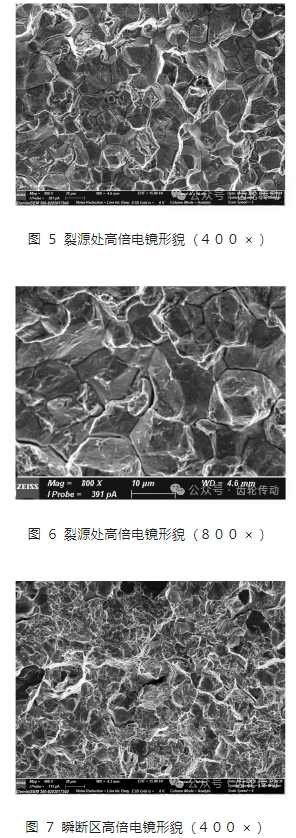
顯微組織分析
將斷裂螺栓縱向剖開取樣,在拋光態下按 GB/T 10561—2005《鋼中非金屬夾雜物含量的測定標準評級圖顯微檢驗法》進行檢驗,結果為:A0.5,B0,C0.5,D0.5,如圖 8 所示,說明非金屬夾雜物輕微,未見異常。
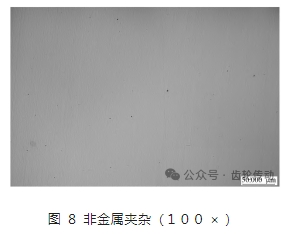
經拋光、侵蝕后進行金相檢查,如圖 9,基體組織為回火索氏體,奧氏體晶粒度約 8 級。值得注意的是,螺栓表面組織為回火索氏體+顆粒狀碳化物,表明存在增碳現象,如圖 10 所示。
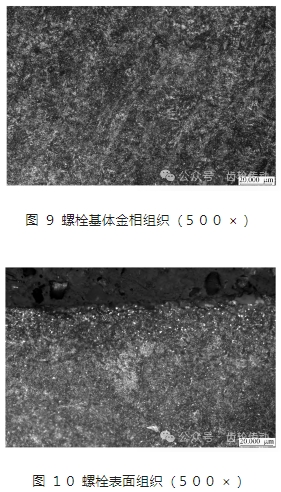
化學成分分析
為確定失效螺栓元素含量是否合格,從螺栓取樣進行化學成分分析,檢驗結果如表 1 所示。可見失效螺栓元素含量符合 JISG 4053—2008《機械構造用合金鋼》中對 SCM435 化學成分的要求。

硬度檢測
失效螺栓硬度檢驗結果如表 2 所示,表面硬度和心部硬度均不符合 GB / T 3098.1—2010《緊固件機械性能螺栓、螺釘和螺柱》中對12.9 級螺栓的要求,其中表面硬度過高與增碳有關。
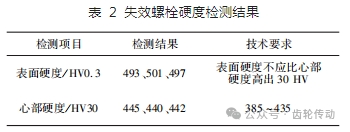
再回火試驗
按 GB / T 3098. 1—2010《緊固件機械性能螺栓、螺釘和螺柱》中規定的試驗方法對失效螺栓進行再回火試驗,工藝參考客戶提供的《螺栓熱處理工藝卡》,回火溫度(460 ± 10)℃ ,保溫時間(60 ± 5)min。試驗前后同一區域硬度下降約40HV,結果不符合標準要求,如表 3 所示,說明失效螺栓在生產制造時存在回火不充分的現象,這也是心部硬度偏高的主要原因。
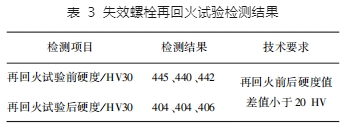
三、失效原因分析與討論
該批螺栓失效特點是裝配后數小時內(短時間內)發生斷裂,并非在車輛運行狀態下失效。根據宏觀棘輪狀脆性斷口和微觀沿晶開裂形貌及晶界雞爪紋等特征,判斷該批次高強度螺栓失效性質符合延遲性開裂特性。延遲開裂是指金屬零件在一定金相組織狀態、靜載荷(正應力)及其他條件下,裂紋萌生并逐步擴展的過程,亦稱靜疲勞。
宏觀棘輪狀多源性斷口是螺栓表面增碳和裝配軸向拉應力及扭轉載荷共同作用的結果,其力學模型如圖 11 所示,另外也表明了螺栓對延遲開裂有較高的敏感性。

螺栓硬度測試結果顯示,表面硬度高出心部硬度 30 HV,依據 GB 3098.1《緊固件機械性能—螺栓、螺釘和螺柱》中 9.11.2.4 條的規定,并結合金相組織分析說明失效螺栓表面已增碳。增碳使螺栓表面硬脆,塑性明顯低于內部,也是引起螺栓脆性斷裂的主要原因。再回火試驗說明,螺栓回火不充分,使螺栓心部硬度偏高,也是心部出現部分沿晶性微觀形貌的原因。
螺栓在裝配過程中頭根部處于扭轉和拉伸應力作用下,在三向不等拉應力狀態下,不利于材料的塑性變形,增加了脆性傾向。同時這些部位截面變化較大,應力集中嚴重、開裂危險性大。當生產工藝調整不當而表面產生增碳時,表面硬度可達到 50 HRC 以上,使螺栓延遲開裂的敏感性大幅增加,失效螺栓的表面硬度在 493~501 HV,技術要求 385~435 HV。
以上述高強度螺栓延遲開裂為例,目前延遲開裂應用最廣泛的是“氫脆”機理,普遍認為工藝氫的引入是此類失效的主因。但在汽車行業大量采用的方式是控制“馬氏體組織”(包括“不充分的 回火組織”)和“持久應力”兩大關鍵要素。原因是高強度零部件延遲開裂的最短時間僅為數 10 s, 對于傳統的“氫致”裂紋機理,該時間內在室溫下完成氫原子(離子)的擴散、聚集、氫氣的析出等過程幾乎是不可能的。因此,認為氫存在于晶界上,可以降低晶界的能量,導致晶界的滑移剪切抗力的降低可使晶界的滑移剪切抗力降低,有利于晶界的滑移,這種機制不需要氫的擴散時間,主要是晶界的黏滯性滑移和裂紋擴展需要時間,故表現出開裂的延遲特性。而這種特性對馬氏體組織及其不充分的回火組織異常敏感,文中螺栓表面增碳和心部硬度偏高都將顯著增加螺栓延遲開裂的敏感性。
四、改進措施
對螺栓淬火后,調整了原來的回火工藝參數,將回火溫度提高到(520±20)℃ ,保溫時間延長至 120 min,淬火爐內保護氣氛控制在 0.30% ~ 0.40% 。將工藝調整后的螺栓人工折斷后進行掃描電鏡分析,斷口呈正常韌窩形貌,如圖 12 所示,硬度測試結果為 386 ~ 388 HV,符合 GB / T 3098.1—2010《緊固件機械性能螺栓、螺釘和螺柱》中對 12.9 級螺栓硬度規定的 385 ~ 435 HV。顯微組織為均勻細回火索氏體,表面無增碳現象,如圖 13 和圖 14 所示。工藝改進后的螺栓未發現延遲開裂現象。
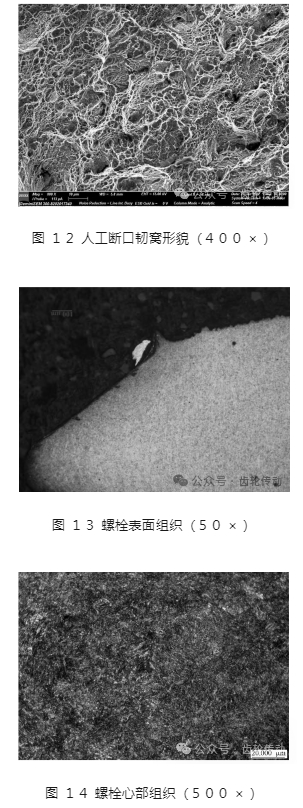
五、結論和建議
該批失效螺栓的斷裂性質為延遲開裂,其原因是心部硬度偏高、表面增碳。為預防類似失效事故再次發生,建議完善螺栓生產過程中的熱處理工藝,適當調整爐內碳勢、回火溫度及回火時間等。另外,在滿足使用工況下的條件下,可考慮降低螺栓性能等級要求。
馬氏體及其不充分的回火組織顯著增加高強度零部件延遲開裂的敏感性,是延遲開裂的必要條件。汽車行業失效分析是一門工程應用技術,建議充分考慮“組織” 和“應力”兩大因素,“氫” 作為重要的致裂因素,工程上應予以回避。
參考文獻略.