隨著數(shù)控機床精密化齒輪加工數(shù)控技術(shù)的快速發(fā)展,人們對數(shù)控機床小模數(shù)齒輪傳動的精度要求不斷升高。數(shù)控機床齒輪的加工精度對生成產(chǎn)品的質(zhì)量具有重要影響。通常情況下,數(shù)控機床小模數(shù)齒 輪在運行過程中,受到部件質(zhì)量、形狀、位置等因素的影響,會產(chǎn)生一定的誤差,例如機床誤差、加工誤差、檢測誤差、傳動誤差等。其中,齒輪的傳動誤差對數(shù)控機床的穩(wěn)定運行具有較大影響。
為了減少數(shù)控機床運行中的誤差,提高加工的精度,相關(guān)的研究人員提出了大量改善方法,應(yīng)用較為廣泛的包括誤差防止技術(shù)與誤差補償技術(shù)。誤差防止技術(shù)通過對零部件進行設(shè)計與裝配,減少數(shù)控機床加工中的誤差源,能夠有效地提高加工精度。然而,誤差防止技術(shù)在應(yīng)用過程中具有較大的局限性,對機床的加工環(huán)境與加工條件要求較高,成本相對來說較高。
為了改善這一不足,筆者設(shè)計了一種數(shù)控機床小模數(shù)齒輪傳動誤差補償方法,通過解耦計算的方式,消除影響數(shù)控機床加工精度的原始誤差。希望通過本文的設(shè)計為數(shù)控機床精密化發(fā)展提供一定的幫助。
一、齒輪傳動誤差補償方法設(shè)計
筆者提出的齒輪傳動誤差補償方法主要包括3個部分:建立滾齒機傳動誤差模型、提取齒輪誤差數(shù)據(jù)、解耦計算齒輪誤差補償值。每個部分的具體設(shè)計步驟如下。
建立滾齒機傳動誤差模型
在本文的數(shù)控機床小模數(shù)齒輪傳動誤差補償方法中,滾齒機傳動誤差模型作為整個方法中重要的組成部分,對數(shù)控機床加工精度具有一定的影響。構(gòu)建滾齒機傳動誤差模型主要包括以下幾部分:分析滾齒機物理結(jié)構(gòu)、基于滾齒機拓撲結(jié)構(gòu)建立坐標系、分析各個部件相對運動的特征矩陣、計算模型參數(shù)。滾齒機傳動誤差模型的建立方式如圖 1所示。
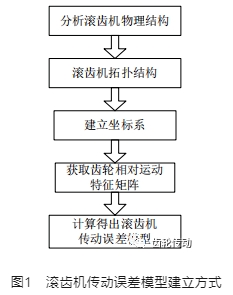
首先,采用有限元分析的方式,獲取數(shù)控機床小模數(shù)滾齒機的物理結(jié)構(gòu),并進行具體的分析,獲取齒輪的定位孔軸線與回轉(zhuǎn)軸線重合狀況,得出滾齒機的拓撲結(jié)構(gòu)與各個部件之間的關(guān)聯(lián)關(guān)系。調(diào)整數(shù)控機床小模數(shù)齒輪上表面的伸長量,得出齒輪立柱中心線間的長度。由于齒輪在傳動過程中受到熱傳導的影響,立柱的溫度逐漸從高溫降為低溫,導致立柱會出現(xiàn)一定程度的彎曲熱變形,為了減少立柱由于熱變形而產(chǎn)生的誤差,將立柱的下端固定在數(shù)控機床的懸臂梁部位,減少傳動中立柱位移造成的溫度影響。
其次,根據(jù)數(shù)控機床滾齒機的刀具分支與工件分支構(gòu)成,以床身為基體,得出滾齒機的拓撲結(jié)構(gòu)。然后設(shè)置滾齒機的工件軸為中間體,拖板、滾刀架、刀具分支分別為 X、Y、Z 軸,建立三維坐標系。基于滾齒機齒輪的相互運動特征,將滾齒機各個部件間的運動轉(zhuǎn)化為坐標系間的變換關(guān)系,獲取滾齒機傳動過程中相對運動的特征矩陣。結(jié)合滾齒機相對運動特征矩陣,計算在傳動過程中滾齒機滾刀軸與工件軸之間的運動關(guān)系,計算公式如下:

式中,ZB表示滾齒機滾刀頭數(shù);ZC表示滾齒機被加工齒輪齒數(shù);vZ表示Z軸向進給速度;vY表示Y軸向進給速度;β表示小模數(shù)齒輪工件螺旋角;λ表示數(shù)控機床滾刀螺旋升角;mn表示滾齒機斜齒輪的法面模數(shù);nB 表示滾齒機的滾刀軸轉(zhuǎn)速;nC表示滾齒機的工件軸轉(zhuǎn)速。通過計算獲取數(shù)控機床滾齒機滾刀軸與工件軸之間的相互關(guān)系,掌握造成傳動誤差的影響因素,對誤差來源進行分類處理。
結(jié)合數(shù)控機床滾齒機的低序體物體陣列原理,對滾齒機的拓撲結(jié)構(gòu)進行陣列運算,獲得滾齒機小模數(shù)齒輪傳動的低序體物體陣列,如表 1所示。
通過上述設(shè)計流程,建立數(shù)控機床滾齒機傳動誤差模型,為后續(xù)的誤差補償方法設(shè)計提供基礎(chǔ)。
提取小模數(shù)齒輪誤差數(shù)據(jù)
為了提高誤差補償處理結(jié)果的精度,采用傳感器采集模型中的各項信息。首先,數(shù)控機床的溫度信息與傳動過程中的位移信息對傳動誤差補償具有重要的作用,采用傳感器測點的方式,在數(shù)控機床距離發(fā)熱源較近的位置進行貼片處理,控制貼片的溫度傳感器數(shù)量大于機床的熱源數(shù)。選定溫度采集點,設(shè)定滾齒機運行的初始溫度,獲取數(shù)控機床熱誤差的變化。調(diào)節(jié)滾齒機導軌與接觸表面的高度距離,采用恒流靜壓導軌技術(shù),計算出數(shù)控機床導軌與滑塊之間的摩擦熱量,公式如下:

式中,QS表示滾齒機單位時間內(nèi)的發(fā)熱量;μ 表示滾齒機傳動過程中的動摩擦系數(shù);FS表示滾齒機導軌接觸面的載荷;J表示滾齒機傳動的熱功當量;vS表示滾齒機傳動過程中導軌的滑動速度。綜合考慮數(shù)控機床小模數(shù)齒輪傳動方式的不同,在提取誤差數(shù)據(jù)時,應(yīng)當控制滾齒機蝸輪與蝸桿之間的相對滑動速度,避免出現(xiàn)傳動效率過低的情況。傳動中,當滾齒機出現(xiàn)升溫現(xiàn)象時,實時記錄溫度的具體變化情況,增大滾齒機齒面的轉(zhuǎn)動速度,提高蝸輪與蝸桿之間齒合面的潤滑程度,獲取滾齒機蝸輪蝸桿的摩擦發(fā)熱量:

式中,QW表示滾齒機蝸輪與蝸桿間產(chǎn)生的摩擦熱量;PW表示滾齒機的轉(zhuǎn)臺功率;η 表示滾齒機傳動效率。根據(jù)計算結(jié)果,提取數(shù)控機床小模數(shù)齒輪傳動過程中的誤差變化數(shù)據(jù)。
解耦計算齒輪誤差補償值
根據(jù)上述提取的滾齒機小模數(shù)齒輪傳動誤差數(shù)據(jù),采用解耦計算的方式,對齒輪輪廓進行誤差補償。首先,考慮數(shù)控機床在加工過程中,砂輪坐標系與工件坐標系之間的轉(zhuǎn)角誤差,分析齒輪由于轉(zhuǎn)角誤差導致的幾何誤差與傳動誤差,進而采取相應(yīng)的誤差補償處理方法。設(shè)定x、y、z 分別為直線X、Y、Z 軸相對于初始坐標系的位移距離,結(jié)合微分變換矩陣的方式,反映初始坐標系的微分變化。
對數(shù)控機床小模數(shù)齒輪進行傳動誤差補償時,首先需要通過一定的方式,獲取滾齒機各運動軸的補償值,結(jié)合微分變換矩陣的原理,計算傳動誤差模型,將砂輪坐標系相對于工件坐標系的轉(zhuǎn)角誤差進行轉(zhuǎn)換,依據(jù)齒輪的輪廓特征,將轉(zhuǎn)角誤差轉(zhuǎn)換到相應(yīng)的運動軸上,從而得到所需的補償值。將補償值插入到數(shù)控系統(tǒng)中,經(jīng)過反饋環(huán)節(jié)的反饋中斷作用,獲取誤差補償值的脈沖信號。當脈沖信號輸入到補償信號伺服控制環(huán)內(nèi)部時,實現(xiàn)誤差補償值脈沖信號的加工補償。
數(shù)控機床小模數(shù)齒輪在傳動過程中還會產(chǎn)生一定的齒距誤差,采用分度圓弧長的度量方式,度量齒合線的增量,計算齒輪的齒距誤差,設(shè)置齒合線的增量為ΔF ,基于解耦計算的方式,計算齒輪轉(zhuǎn)角誤差對應(yīng)的分度圓弧長誤差為:
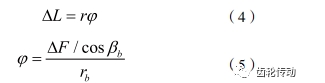
式中,βb表示小模數(shù)齒輪基圓的螺旋角;φ 表示小模數(shù)齒輪的轉(zhuǎn)角誤差;r表示齒輪基圓的半徑;rb表示齒輪分度圓的半徑。通過計算,獲取齒輪分度圓弧長與轉(zhuǎn)角誤差的對應(yīng)關(guān)系。
調(diào)整小模數(shù)齒輪的運動姿態(tài),對齒輪實施與傳動誤差方向相反、大小相等的補償運動,抵消小模數(shù)齒輪與工件之間的轉(zhuǎn)角誤差,使齒輪的磨削面與工件的加工表面達到重合。修正數(shù)控機床小模數(shù)齒輪的數(shù)控指令以及傳動軌跡,在工件坐標系內(nèi)獲取齒輪中心位置的變化曲線,通過調(diào)整齒輪的傳動誤差方向及大小,實現(xiàn)數(shù)控機床的高精度加工。
二、實驗與結(jié)果分析
綜合上述內(nèi)容,為了進一步對數(shù)控機床小模數(shù)齒輪傳動誤差補償方法的可行性作出客觀分析,進行如下實驗測試。
實驗準備
采用 PT100 溫度傳感器、1 套激光干涉儀、齒輪傳動模擬量信號采集卡、數(shù)控滾齒機及若干導線。用溫度傳感器采集若干數(shù)控機床小模數(shù)齒輪運行過程中的溫度信息與位移信息,在機床中布設(shè) 8 個測點,測試齒輪傳動的實時溫度并進行記錄。利用齒輪傳動模擬量信號采集卡采集電壓信號,并將電壓值轉(zhuǎn)換為溫度值。通過激光干涉儀,測量機床刀架處的位移變形情況,并將以上獲取到的數(shù)值記錄到傳動誤差模型中。本次實驗的目標對象為型號為MT2418的滾齒機,滾齒機上包括驅(qū)動安裝工件的頂尖軸,滾齒機加工對象的模數(shù)為 1,齒數(shù)為 50,壓力角為 25°,小模數(shù)齒輪的螺旋角度數(shù)為 24.5°,計算工件傳動過程中的開環(huán)傳遞函數(shù):
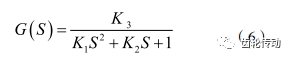
式中,K1表示數(shù)控機床伺服電機軸的轉(zhuǎn)動慣量;K2表示扭轉(zhuǎn)剛度;K3表示阻尼系數(shù);S表示齒輪傳動降速比常數(shù)。
結(jié)果分析
根據(jù)上述計算結(jié)果,結(jié)合坐標變換的方式,設(shè)置小模數(shù)齒輪傳動的周期為一周,獲取數(shù)控機床小模數(shù)齒輪傳動進行誤差補償前后的轉(zhuǎn)角誤差曲線變化情況,如圖 2、圖 3所示。
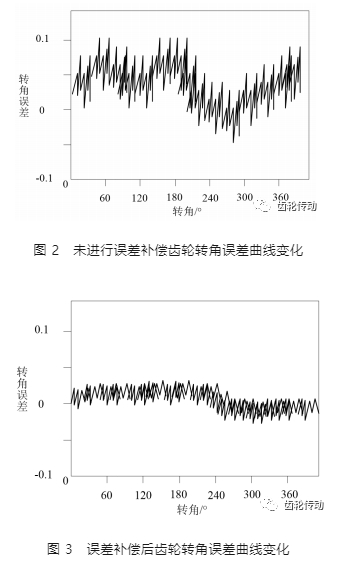
由圖 2、圖 3 可知,未經(jīng)過誤差補償處理的小模數(shù)齒輪,在傳動過程中,轉(zhuǎn)角誤差的變化幅度較大,整體運行較不穩(wěn)定;經(jīng)過文中提及的誤差補償方法處理后,有效降低了齒輪的轉(zhuǎn)角誤差,在傳動過程中平穩(wěn)性較強,能夠?qū)崿F(xiàn)數(shù)控機床小模數(shù)齒輪的高精度加工。
三、結(jié)語
綜上所述,為了提高數(shù)控機床小模數(shù)齒輪加工的精度,針對加工中產(chǎn)生的誤差,提出了數(shù)控機床小模數(shù)齒輪傳動誤差補償方法。該誤差補償方法適用性較強,能夠降低齒輪傳動過程中產(chǎn)生的轉(zhuǎn)角誤差,且成本較低,彌補了傳統(tǒng)誤差防止方法的不足,在一定程度上延長了數(shù)控機床的使用壽命。
參考文獻略.